The Ultimate Guide to Die Casting Parts
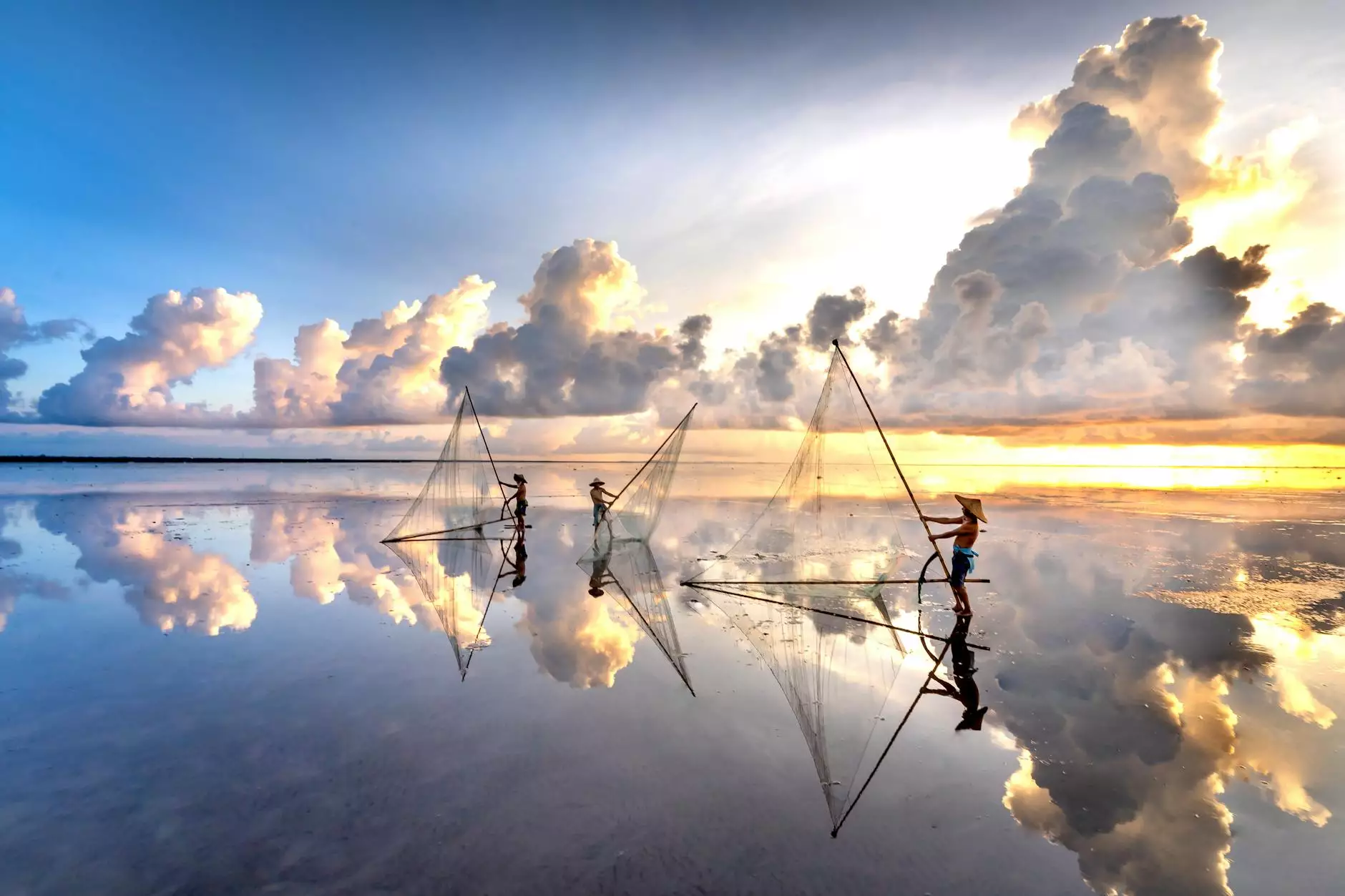
In the vast landscape of manufacturing, die casting parts play a crucial role in various industries, including automotive, aerospace, electronics, and consumer goods. As a leading metal fabricator, particularly in the realm of die casting, Deep Mould stands out through innovation, quality, and excellence in production. In this comprehensive guide, we will delve deep into die casting parts, their applications, benefits, and how they can significantly enhance the efficiency of manufacturing processes.
What is Die Casting?
Die casting is a manufacturing process that involves forcing molten metal into a mold cavity under high pressure. This technique is known for producing parts with excellent dimensional accuracy and surface finish. The molds, or dies, are typically made of steel and can be reused multiple times, making them particularly cost-effective for high-volume production.
Types of Die Casting Processes
There are primarily two types of die casting processes:
- High-Pressure Die Casting (HPDC): In this method, molten metal is injected into the die at high speed under considerable pressure. This enables the production of intricate and finely detailed components.
- Low-Pressure Die Casting: This technique involves using a lower pressure to fill the mold, which is often used for larger parts. It allows for better metal flow and reduced turbulence, leading to fewer defects.
Benefits of Using Die Casting Parts
Die casting parts offer numerous advantages that make them a preferred choice for many manufacturers:
- Precision and Accuracy: Die casting provides a high dimensional stability, offering parts that require minimal finishing.
- Complex Shapes: This process allows for intricate designs that would be impractical with other manufacturing methods.
- Enhanced Strength: Die cast parts can be stronger than those created through other processes, suitable for high-stress applications.
- Cost-Effectiveness: Especially for large production runs, die casting can be more economical as the mold can be reused, reducing material waste.
- Surface Finish: The products often require little to no additional treatment, which saves time and labor costs.
Common Applications of Die Casting Parts
Die casting is utilized in various industries, including:
1. Automotive Industry
In the automotive sector, die casting parts are crucial for producing components such as:
- Engine blocks
- Transmission cases
- Throttle bodies
- Interior and exterior trim pieces
2. Aerospace Industry
The aerospace sector values die casting for its:
- Lightweight components
- Durability under harsh conditions
- Complex geometries that improve aerodynamics
3. Electronics
In electronics, die casting allows for:
- Protection casings
- Housing for electrical components
- Heat sinks that dissipate heat efficiently
4. Consumer Goods
Everyday consumer products often utilize die casting for:
- Kitchen appliances
- Furniture parts
- Sporting goods
Materials Used in Die Casting
The choice of material is pivotal in the die casting process. Common metals used include:
- A Zinc Alloys: These are favored for their excellent castability and good mechanical properties.
- Aluminum Alloys: Known for their low density and high strength-to-weight ratio, aluminum die casting parts are widely used.
- Magnesium Alloys: These alloys provide an even lighter alternative while retaining strength.
- Lead Alloys: Although less common due to environmental concerns, lead offers excellent flow and is typically used for specialty products.
Quality Control in Die Casting
Ensuring the quality of die casting parts is paramount. At Deep Mould, rigorous quality control measures are implemented throughout the manufacturing process, including:
- Material Inspection: All raw materials undergo strict inspection before use.
- Process Monitoring: Continuous monitoring of temperature and pressure during casting ensures optimal conditions.
- Dimensional Checks: Regular checks confirm parts meet specified tolerances and dimensional requirements.
- Surface Quality Inspection: Final products are inspected for surface blemishes and defects.
Choosing the Right Die Casting Partner
When selecting a die casting manufacturer, consider the following factors to ensure you partner with the best:
- Experience and Expertise: Look for a company with a proven track record in die casting.
- Capability and Technology: Ensure they utilize the latest technology and have the capability to deliver high-quality parts efficiently.
- Customer Service: A responsive and communicative partner will help address any concerns or questions that arise.
- Quality Assurance Processes: Understand their quality control mechanisms to ensure that you receive defect-free products.
- Pricing Structure: While cost should not be the only deciding factor, it is essential to find a partner that provides value for money.
The Future of Die Casting Parts
The landscape of manufacturing is continually evolving, with die casting parts becoming even more significant. Innovations in materials, automation, and smart manufacturing are shaping the future of this industry. As manufacturers seek to improve efficiency and reduce costs, die casting presents an ideal solution due to its adaptability and scalability.
Conclusion
Die casting parts have transformed the manufacturing sector by providing reliable, precise, and cost-effective solutions for various industries. With its numerous benefits and applications, die casting continues to hold a pivotal role in shaping the products we use daily. As we advance into a new era of technology and innovation, staying ahead in the die casting domain is essential for manufacturers looking to thrive.
At Deep Mould, we pride ourselves on being at the forefront of this industry, committed to producing high-quality die casting parts that meet the evolving demands of our clients. For more information about our services and expertise in die casting parts, please visit our website at deepmould.net.