Injection Molding of Plastics: A Comprehensive Guide
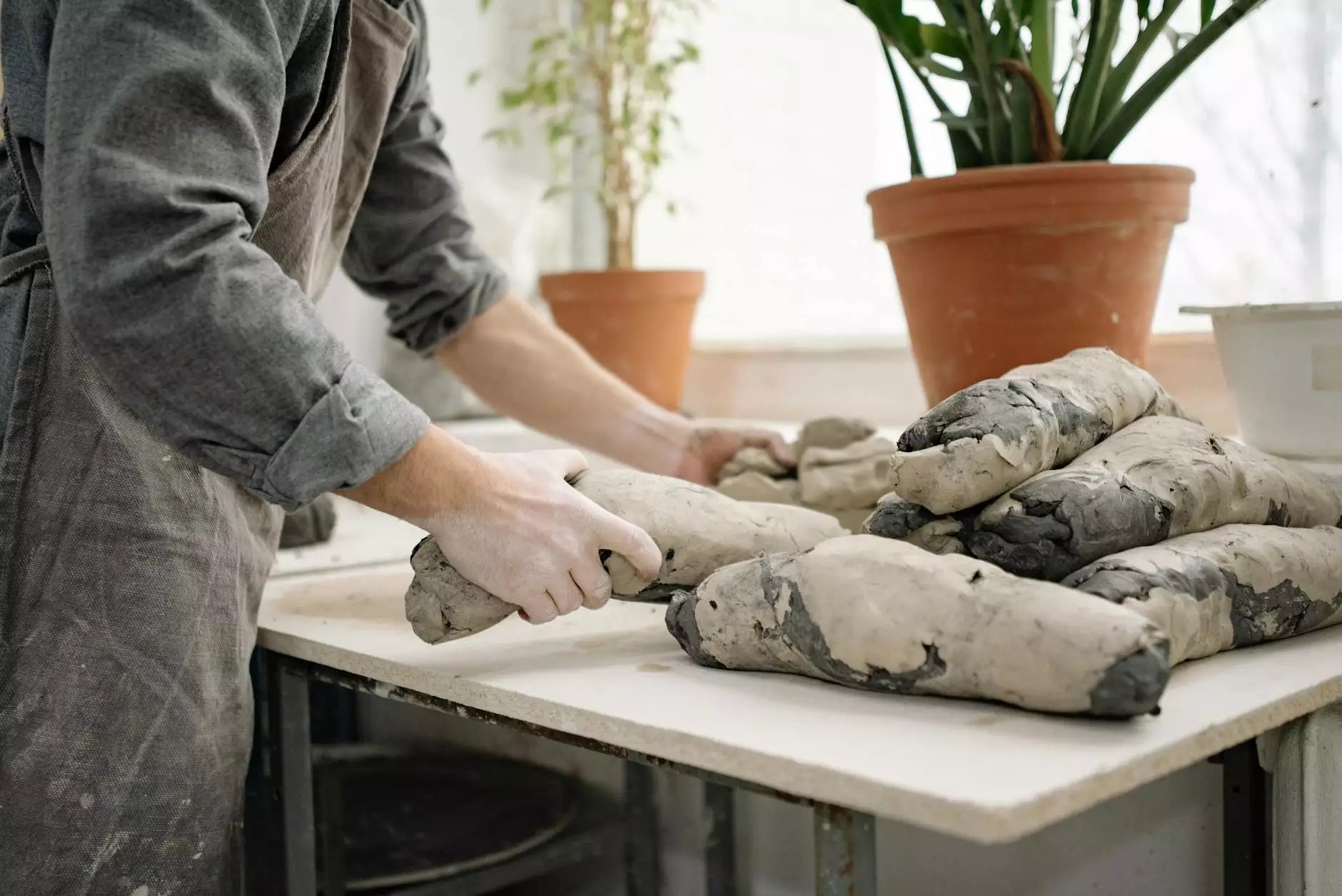
Injection molding of plastics is a revolutionary process that allows for the rapid and efficient manufacturing of complex plastic components. This technology has transformed the way industries develop products, ranging from consumer goods to intricate parts used in automotive and medical applications.
What is Injection Molding?
Injection molding is a manufacturing process in which molten plastic material is injected into a mold, where it cools and solidifies to form a specific shape. This process combines high precision with repeatability, making it ideal for producing large quantities of parts with tight tolerances.
The Injection Molding Process Explained
The injection molding process can be broken down into several key stages that ensure the final product meets the quality and precision required by various industries.
1. Material Selection
The selection of appropriate plastic materials is crucial. Common choices include:
- Polypropylene (PP) - Versatile and cost-effective.
- Polyethylene (PE) - Offers good chemical resistance.
- Polystyrene (PS) - Lightweight and easy to process.
- ABS (Acrylonitrile Butadiene Styrene) - Durable and impact-resistant.
2. Designing the Mold
The mold is typically made from steel or aluminum and is designed to withstand the high pressures involved in the injection process. The design must accommodate for:
- Parting lines
- Draft angles
- Cooling channels
- Gate locations
3. Heating and Injecting
Once the materials are selected and the mold is created, the plastic pellets are heated until they reach a molten state. This molten plastic is then injected into the mold via a screw or a plunger, filling the cavity and taking its shape.
4. Cooling and Ejection
After the mold is filled, it is cooled, allowing the plastic to harden. Once solidified, the mold opens, and the finished part is ejected. This stage is essential to achieving the desired properties in the finished product.
Benefits of Injection Molding of Plastics
There are several advantages associated with the injection molding of plastics process, making it a preferred choice for many manufacturers:
Cost-Effectiveness
Though initial setup costs for injection molding can be high, the cost per unit dramatically decreases with mass production. This efficiency significantly benefits large-scale production runs.
Design Versatility
Injection molding offers unparalleled design flexibility, allowing manufacturers to create intricate designs that would be impossible or prohibitively expensive with other methods.
Material Efficiency
With recycling capabilities and minimal waste production during the manufacturing process, injection molding is one of the most environmentally friendly methods available.
High Precision and Consistency
The repeatability of the injection molding process ensures that products maintain a high degree of accuracy, essential for applications requiring strict tolerances.
Applications of Injection Molding
The injection molding of plastics is used across various sectors, including but not limited to:
Consumer Products
Many everyday items, from plastic containers to toys, are produced using injection molding techniques due to their affordability and ability to mass-produce designs.
Automotive Industry
Injection molding plays a critical role in automotive parts, including dashboards, panels, and various internal components, contributing to weight reduction and assembly efficiency.
Medical Devices
The sterile and precise nature of injection molding makes it ideal for manufacturing medical devices, such as syringes, anesthesia masks, and orthopedic implants, where quality and consistency are paramount.
Electronics
Electrical enclosures and connectors are often produced via injection molding, allowing for intricate designs and shielding that protect sensitive components.
The Future of Injection Molding
As technology progresses, the injection molding of plastics continues to evolve. Innovations such as 3D printing and advances in material science are impacting the industry, enabling manufacturers to achieve even greater efficiencies and capabilities.
Emerging Technologies
Several emerging technologies promise to enhance the injection molding process, including:
- Advanced Robotics - Improving precision and reducing labor costs.
- Smart Manufacturing - Utilizing IoT for real-time monitoring and predictive maintenance.
- Bioplastics - Offering sustainable alternatives to traditional plastics.
Choosing the Right Injection Molding Partner
For businesses looking to leverage the advantages of injection molding, choosing the right partner is crucial. Here are some guidelines:
1. Experience and Expertise
Look for partners with a strong track record in injection molding. A company with extensive experience can navigate the challenges of design and production efficiently.
2. Quality Assurance Processes
Ensure that the provider has rigorous quality control processes in place. Consistency in production is key in maintaining high-quality standards.
3. Technology and Equipment
A company that invests in modern technology and equipment will likely provide better efficiency and quality, allowing for faster turnaround times.
4. Flexibility and Customer Service
Good communication and customer service are essential. A responsive partner can adapt to changes in production needs or design modifications.
Conclusion
The injection molding of plastics is a fundamental process that has reshaped various industries. Its efficiency, flexibility, and cost-effectiveness make it invaluable for manufacturers across the globe. As advancements in technology continue to emerge, the potential for injection molding to innovate and adapt will only grow, presenting exciting opportunities for businesses willing to embrace its capabilities.
To learn more about how deepmould.net can assist you with your injection molding needs, explore our website or contact us today!