The Evolution and Impact of Industrial Molds in Business
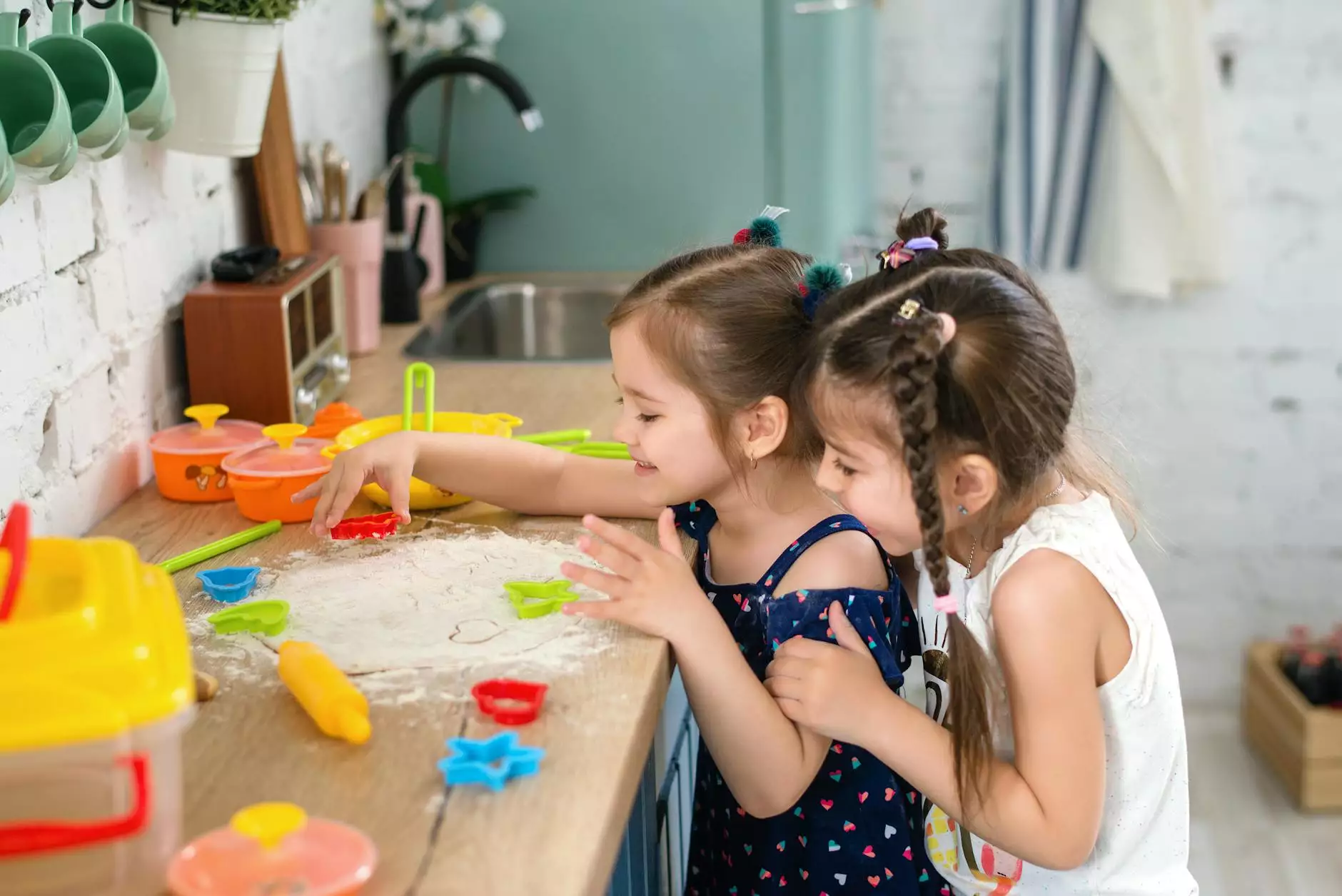
In the world of manufacturing, the role of industrial molds cannot be overstated. These essential tools are the backbone of many industries, enabling the production of a vast array of products efficiently and effectively. At hanking-mould.com, we understand the unique requirements of businesses that count on precision and quality in their manufacturing processes. This article dives deep into the realms of business associated with industrial molds, emphasizing their importance, applications, and the innovations in this field.
Understanding Industrial Molds
Industrial molds are specific types of tooling used primarily for shaping materials, most commonly plastics and metals. These molds are crucial for creating products with complex geometries and high precision. The process often involves several manufacturing techniques, including:
- Injection Molding: A widely used method where molten material is injected into a mold cavity to produce components.
- Blow Molding: This technique forms hollow parts by inflating a heated plastic tube until it fills a mold.
- Compression Molding: Material is placed into a heated mold cavity and then pressed to shape it into a desired form.
- Thermoforming: A process where plastic sheets are heated and shaped over a mold.
The Importance of Plastic Mold Makers
As businesses continue to seek efficiency and cost-effectiveness, the role of plastic mold makers has become paramount. These specialists focus on creating high-quality molds tailored to specific product needs, contributing greatly to various sectors such as automotive, consumer goods, and electronics.
Advantages of Using Custom Molds
Custom molds provide several key benefits that are essential for manufacturers:
- Precision and Consistency: Custom molds ensure that each product meets exact specifications, reducing waste and variability.
- Cost-Effectiveness: While the initial investment may be higher, the long-term savings from reduced scrap rates and faster production times significantly outweigh costs.
- Flexibility: Tailored molds can be adapted to accommodate new designs or product adjustments without a complete overhaul of the production line.
- Enhanced Product Quality: High-quality molds lead to improved product durability and performance, critical in competitive markets.
Plastic Injection Mould Manufacturer: The Backbone of Production
A plastic injection mold manufacturer plays a crucial role in the supply chain, transforming raw materials into finished products ready for market. This process involves several key stages:
1. Design and Engineering
The journey begins with the design phase, where engineers collaborate with clients to create mold designs that meet their specific needs. Advanced CAD software and simulation tools are utilized to visualize the final product and identify potential manufacturing challenges.
2. Prototype Development
Once a design is finalized, a prototype is developed to assess its feasibility. This stage allows manufacturers to test the design and make necessary adjustments before mass production begins, ensuring quality and functionality.
3. Production of Molds
After prototypes have been validated, the manufacturing of the molds begins. This stage involves precision machining, often using CNC technology, to create molds that can withstand the high pressures and temperatures of the injection molding process.
4. Testing and Quality Assurance
Quality checks are integral at this stage. Testing ensures that molds function as intended and meet industry standards for safety, durability, and performance.
5. Mass Production
With molds ready, the actual production of parts can begin. Injection molding machines inject molten plastic into the molds, allowing for rapid production of high-quality components.
Applications of Industrial Molds
Industrial molds are used across various industries, underscoring their versatility and significance:
Automotive Industry
In the automotive sector, industrial molds produce everything from dashboard components to exterior body panels. The ability to create complex shapes efficiently makes injection molding a preferred manufacturing method for car manufacturers worldwide.
Consumer Goods
Everyday products, such as containers, toys, and appliances, benefit from industrial molds. Custom molds are key to developing innovative designs that attract consumers and deliver functionality.
Medical Devices
The production of medical device components requires utmost precision and hygiene. Industrial molds yield parts that must meet stringent regulatory requirements, ensuring both safety and efficacy.
Electronics Manufacturing
In the electronics sector, molds are used to create housings, connectors, and internal components. As technology evolves, manufacturers rely on innovative molding solutions to keep pace with rapid advancements.
Future Trends in Industrial Molds
As technology progresses, the field of industrial molds continues to innovate. Here are some future trends that businesses should keep an eye on:
1. 3D Printing in Mold Making
3D printing technology is revolutionizing mold design and production, enabling rapid prototyping and reduced lead times.
2. Sustainability Initiatives
With increasing awareness of environmental issues, manufacturers are focusing on sustainable materials and processes, including the use of biodegradable plastics in molding operations.
3. Advanced Materials
Future trends indicate a shift towards the use of high-performance materials that enhance mold durability and performance, providing greater resistance to wear and thermal expansion.
4. Automation and Smart Manufacturing
The integration of automation technologies and IoT in manufacturing processes is enhancing productivity and accuracy, allowing for real-time monitoring and maintenance of molds.
Conclusion
The significance of industrial molds in modern manufacturing is undeniable. As industries evolve, the demand for precision, efficiency, and quality will only increase. At hanking-mould.com, we are committed to delivering state-of-the-art plastic mold making and injection molding solutions that meet the highest standards. By understanding the structure, benefits, and future of industrial molds, businesses can strategically position themselves for success in a rapidly evolving marketplace.
Investing in quality molds is not just about production; it's about shaping the future of your products and, ultimately, your business.